ATEX Global
A complete and digitized service, which allows creating or reviewing the Explosion Protection Document, inspections of all devices with information in real-time.
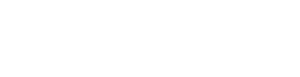
INNOVATION TO ASSURANCE SAFETY
IN ATEX / DSEAR or IECEx ATMOSPHERES
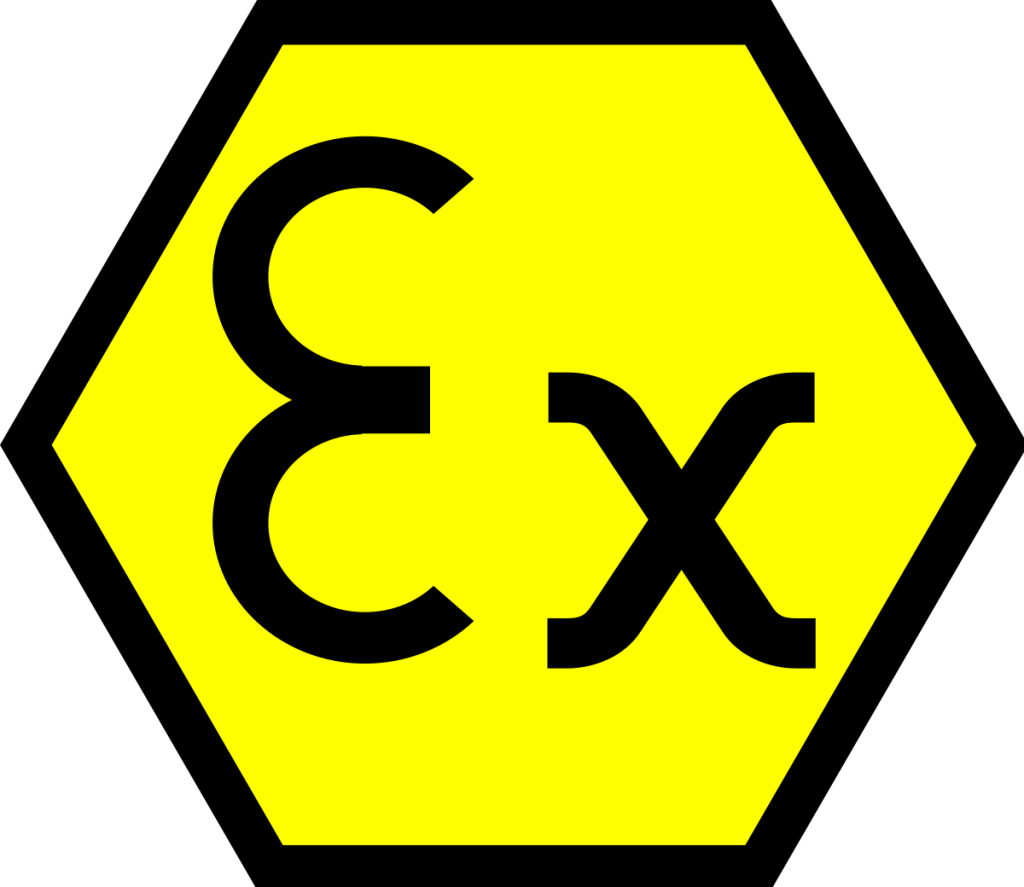
Technological innovation in guaranteeing safety in ATEX / DSEAR or IECEx atmospheres is a question that must be addressed not only in the petrochemical industry but in several industries susceptible to explosive atmospheres. There are many industrial activities in which explosive atmospheres (ATEX) exist due to the combustible/flammable nature of the substances that these industries process or store.
Electricity production
Chemical industry
Waste water treatment
Gas distribution
Wood processing
Paint and coating
Agriculture
Metallurgy
Food industry
Pharmaceutical industry
Recycling
Refineries
Landfills
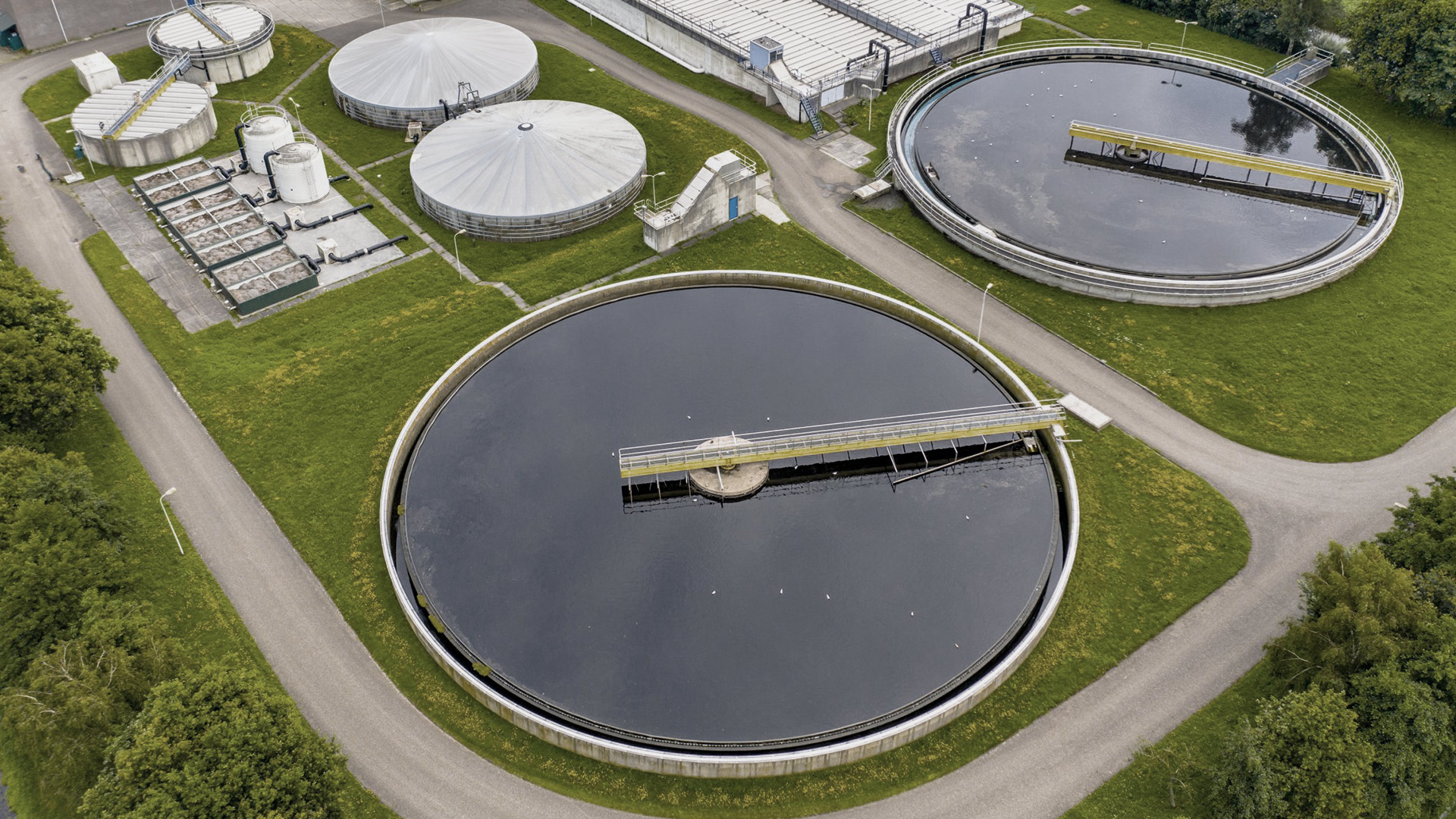
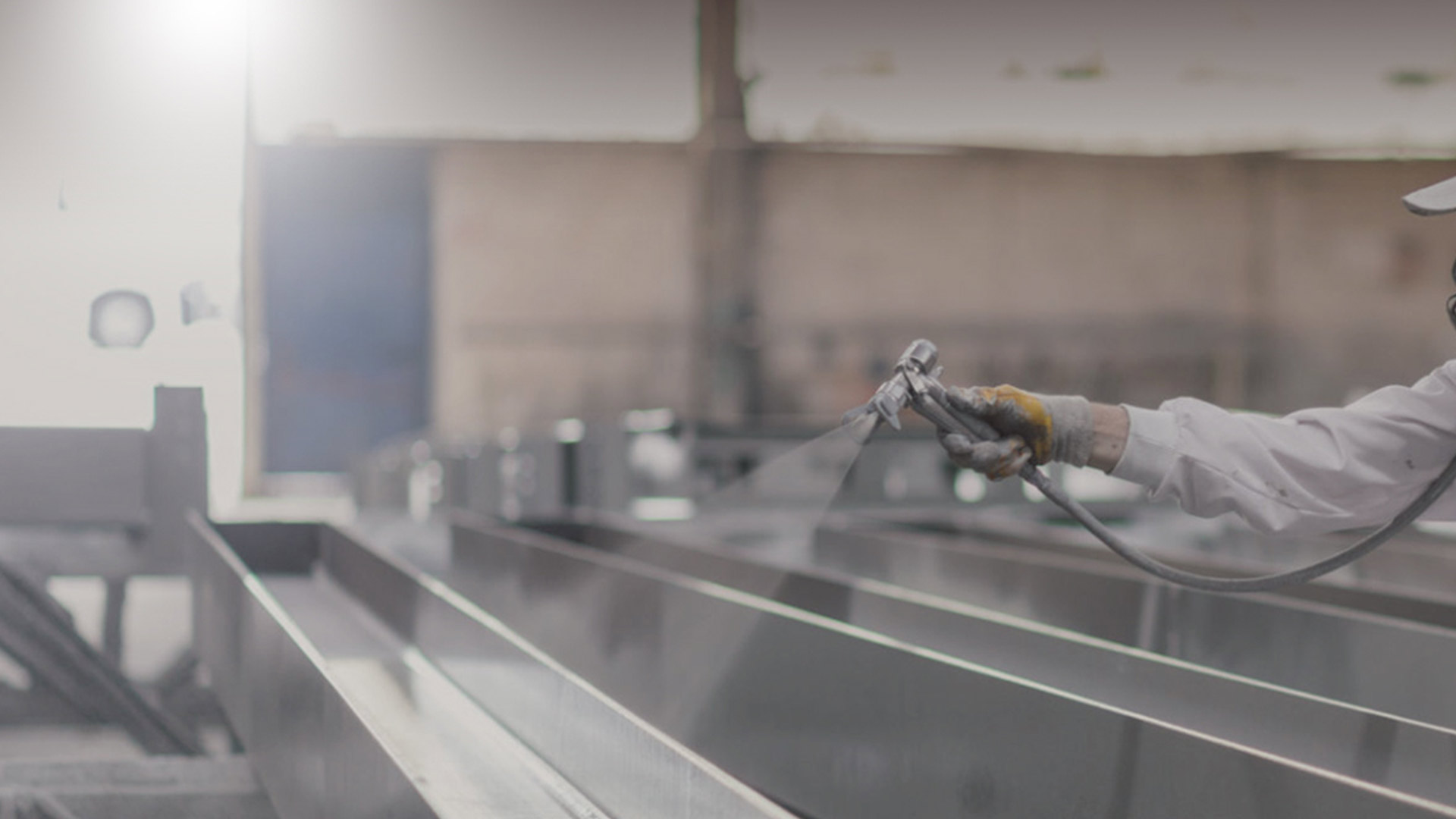
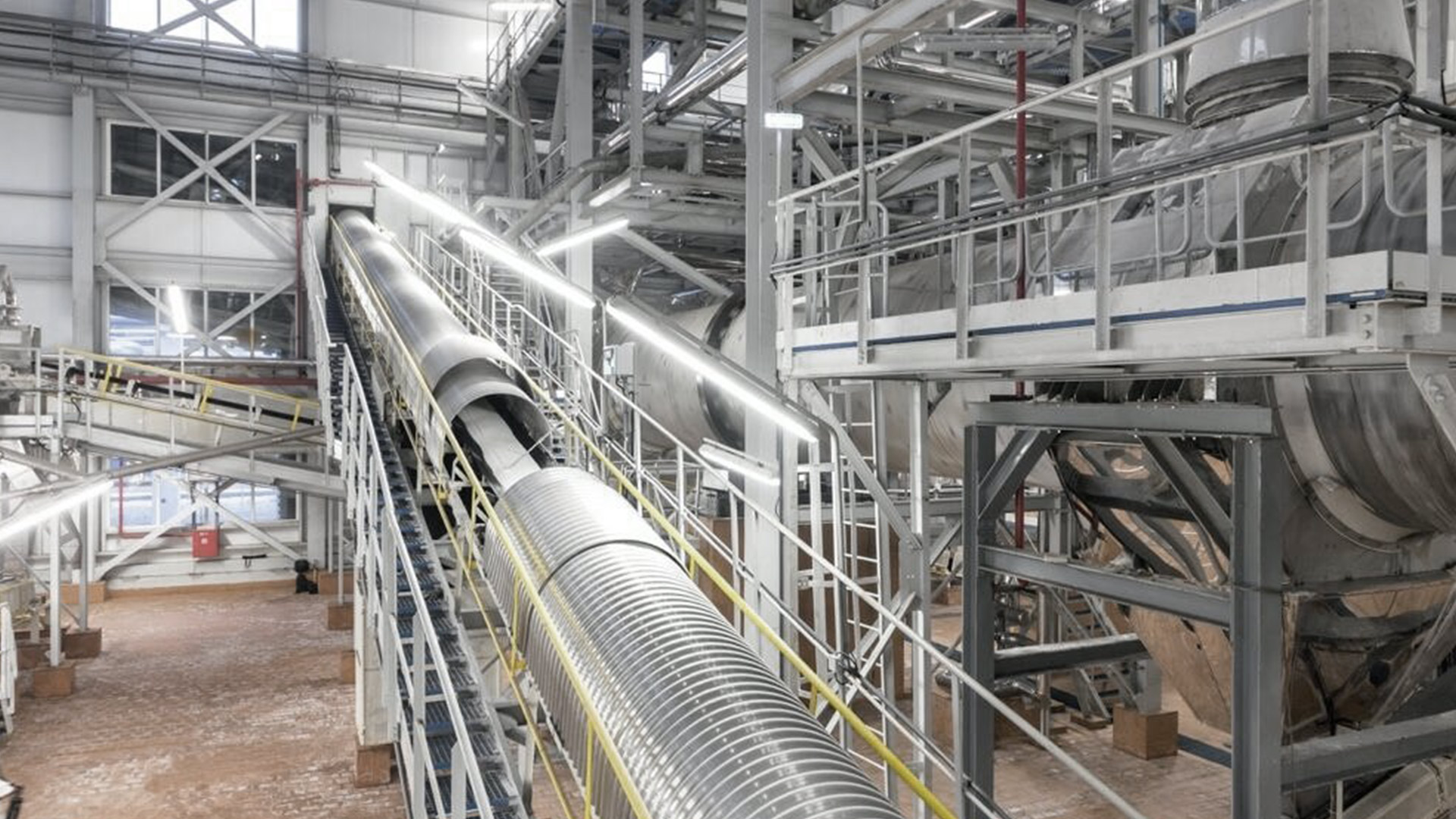
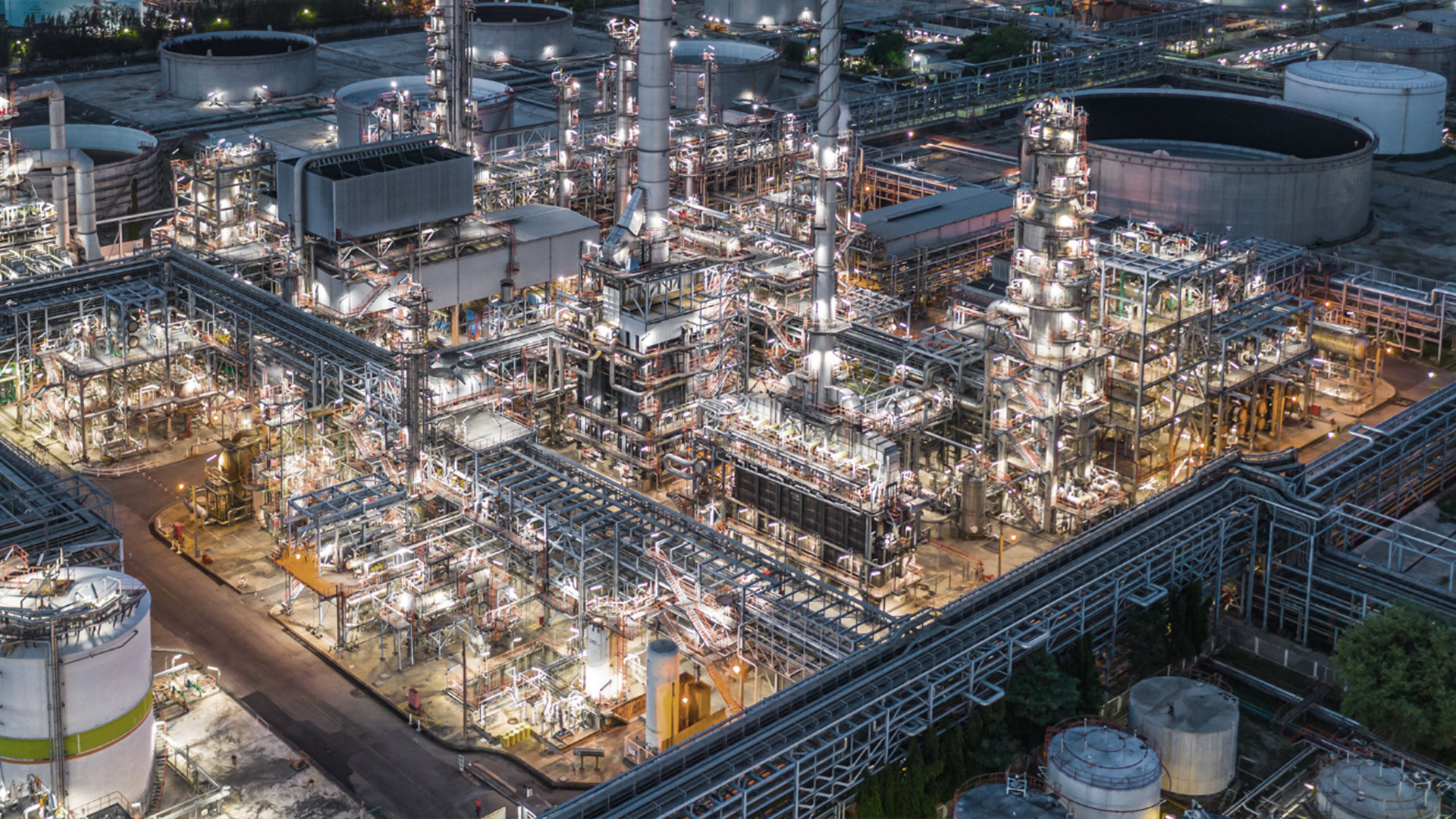
CENTRALIZING INFORMATION SAVES TIME IN RISKY SITUATIONS
The use of technologies offers a more effective predictive and preventive analysis for risk situations in each ATEX area, anticipating possible risks and favoring decision-making in emergency situations.
The response time is immediate as all information is centralized, organized, and accessible to all responsible parties.
ADVANTAGES:
Preventing explosions in potentially explosive atmospheres
Mitigating the risk of accidents
Ensure regulatory compliance
Reduced cost of fines
Reduced insurance premiums
Enhance your reputation as a safe and reliable company
ATEX, DSEAR, and IECEx are all related to the safety of equipment and systems used in potentially explosive atmospheres. ATEX is a European directive, DSEAR is a set of UK regulations, and IECEx is an international certification system, all working towards the same goal of preventing explosions and ensuring the safety of workers in hazardous environments.
These objectives are achieved through a series of specific requirements, including the classification of areas, risk assessment of personal injury and material damage, the inspection of equipment and systems, the implementation of appropriate safety measures, and the training of employees.
ATEX Manual revised whenever there are significant changes that affect the safety of operations.
Frequency of inspections of equipment installed in hazardous areas.
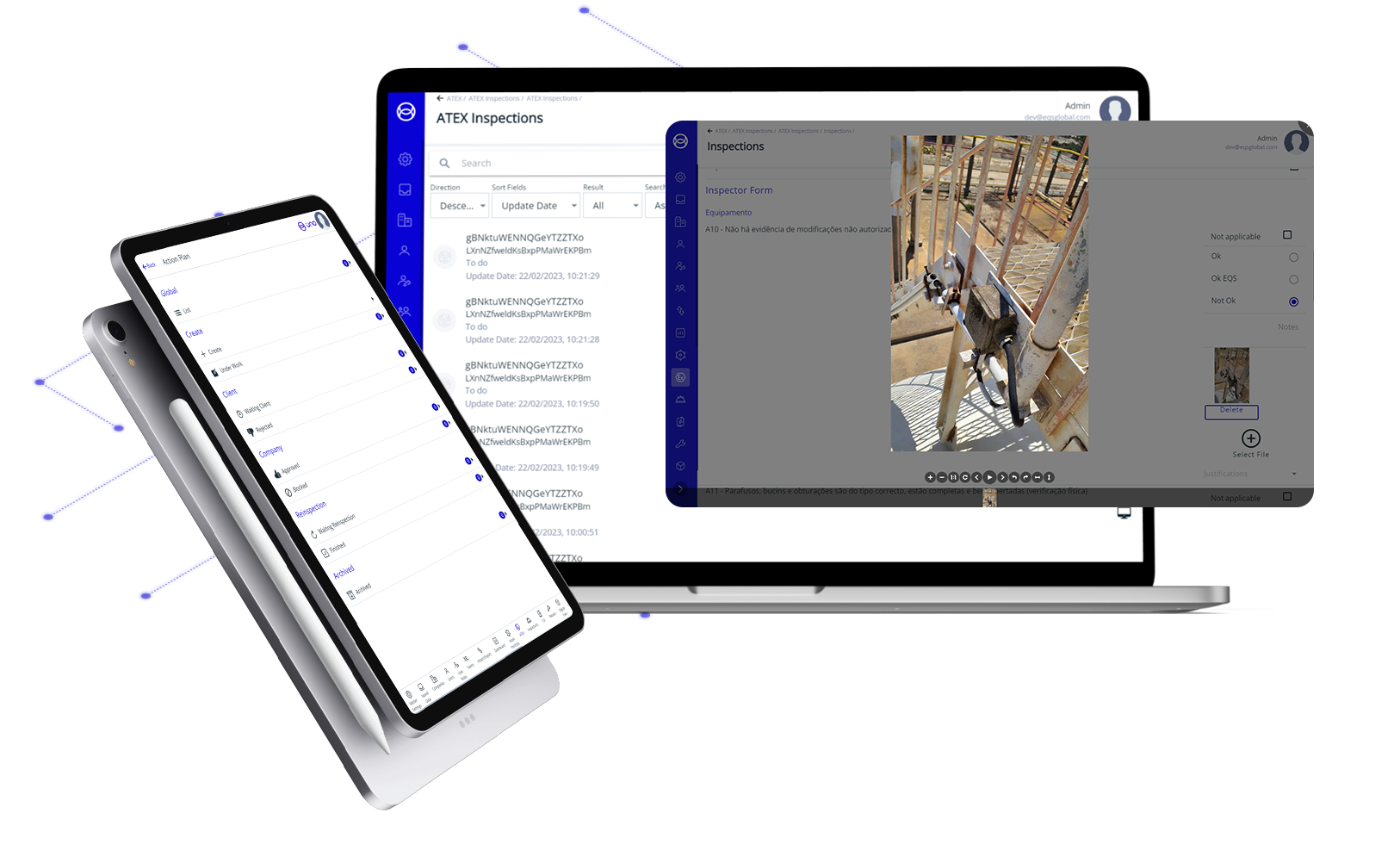
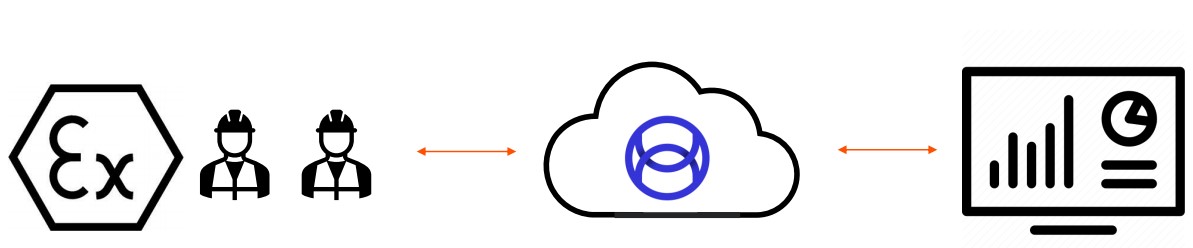
The use of digital tools makes it possible to optimize the flow of information and obtain data in real-time, such as KPIs, high-risk anomalies, and action plans.
Auditable
Safe
Mobility
Digital Transformation that Improves an Operational Safety
ATEX PetrochemicalCASE STUDY
The petrochemical company needed to:
- Review the Explosion Protection Manual
- Detailed inspection of electrical, non-electrical, and instrumentation equipment within hazardous areas
- Gap analysis and implementation of minor repairs
- Implementation of a reinspection system
0
0
0
0
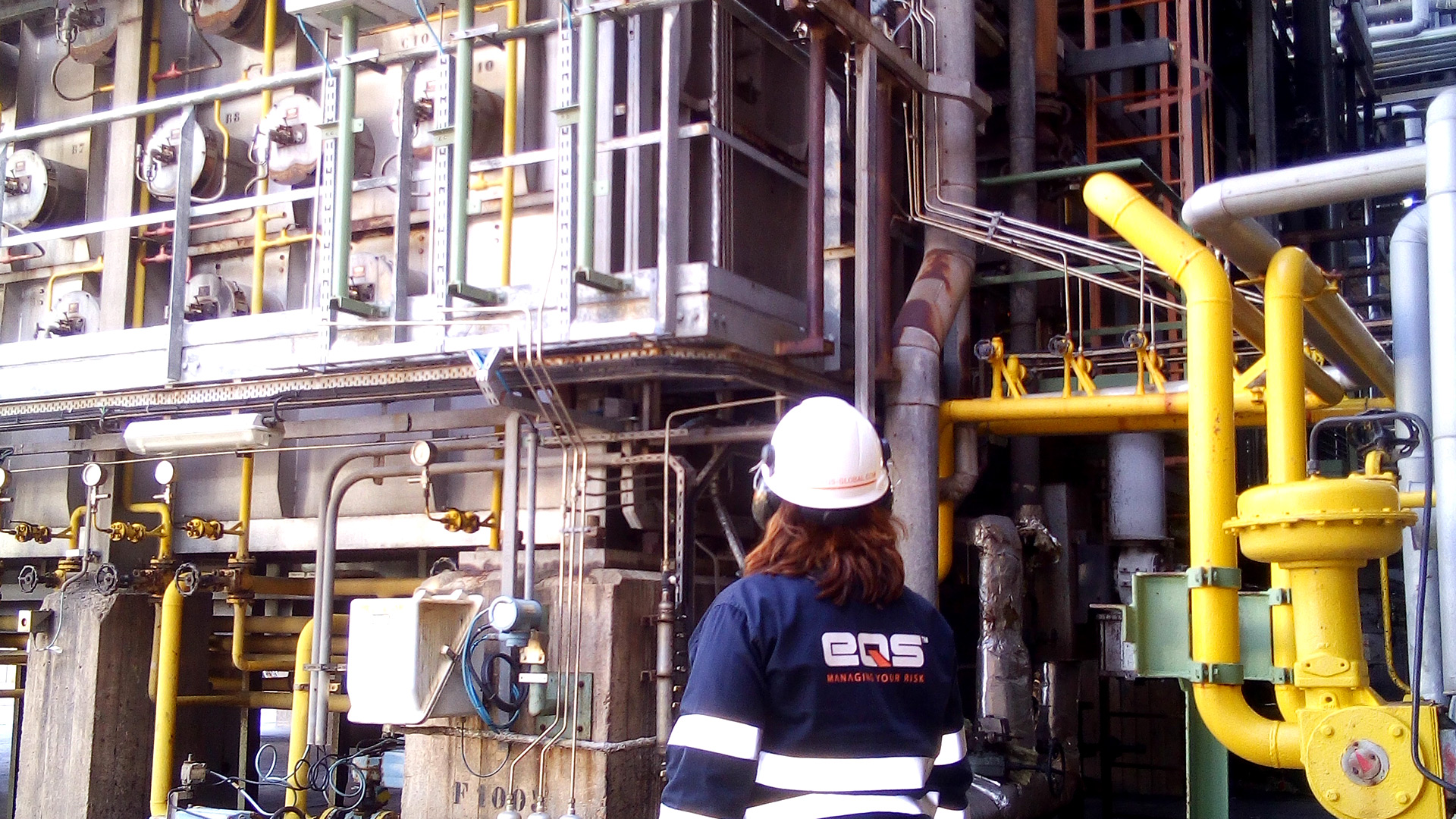
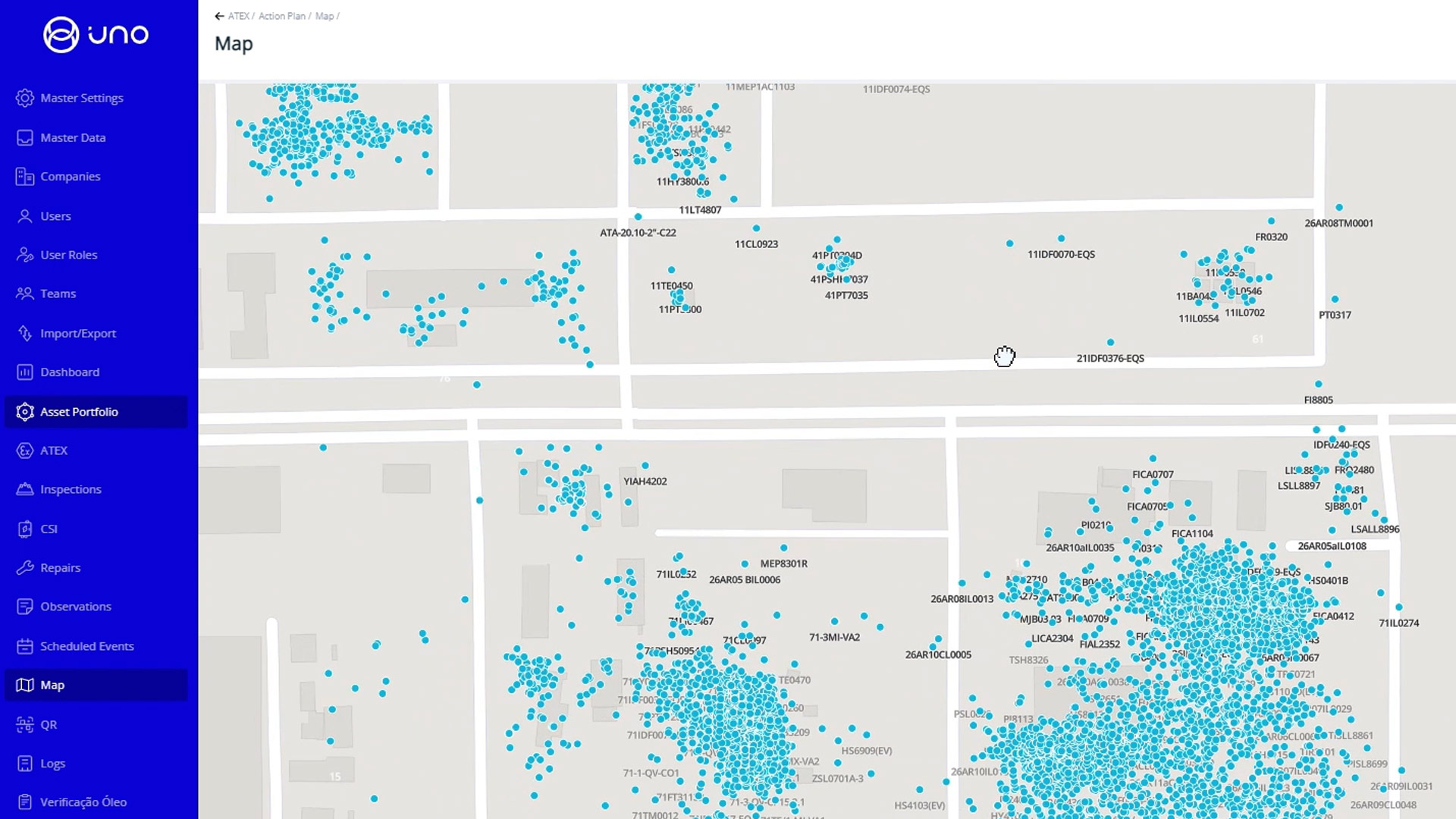
No projeto estiveram envolvidos:
- 2 ATEX experts
- 14 inspetors and backoffice technicians
Were developed:
- more than 23.000 inspections and equipments
- more than 68.000 fitness for purpose (gap analysis)
- more than 49.000 action plans
- more than 2.000 earth continuity measurements
- placed more than 500 identification smart tags
- placed more than 1,600 cable tags
Descrição dos trabalhos
CREATION/REVISION OF THE ATEX MANUAL
Tasks performed:
- Explosivity analysis of various dust samples
- Operational data analysis
- Simulations using Phast software
- Risk assessment of damage and material
- Documental Revision
- Revision of area classification drawings
FIELD INSPECTION
Inspections were carried out in accordance with the IEC 60079 standard on the:
- electrical equipment
- Non-Electrical equipment
- Instrumentation equipment
The ATEX module was used to carry out the inspections, collecting all the evidence (photographs, videos, text).
All actions and indicators are generated in real time.
GAP IDENTIFICATION AND ACTIONS RECOMMENDATIONS
By geo-referencing the equipment and comparing it with the plans produced, we check that the equipment is in accordance with the needs of the site.
During the inspection we check all the applicable points of the IEC standard checklists, ensuring that anomalies are identified and can be repaired.
ACTION PLAN + REINSPECTION
For each one of the identified GAP, were defined mitigation actions.
After the action was implemented, re-inspections were carried out.
PERIODIC INSPECTIONS
Periodic inspections are essential to ensure that installations are kept in satisfactory condition.
The ATEX module allows us to define inspection periods, ensuring that we have vision and control over inspections.
TRAINING
Training activities were carried out (legal obligation)
- 3 training sessions were held
- 2 online training actions were made available
Walking Together
For The Most Demanding Industries
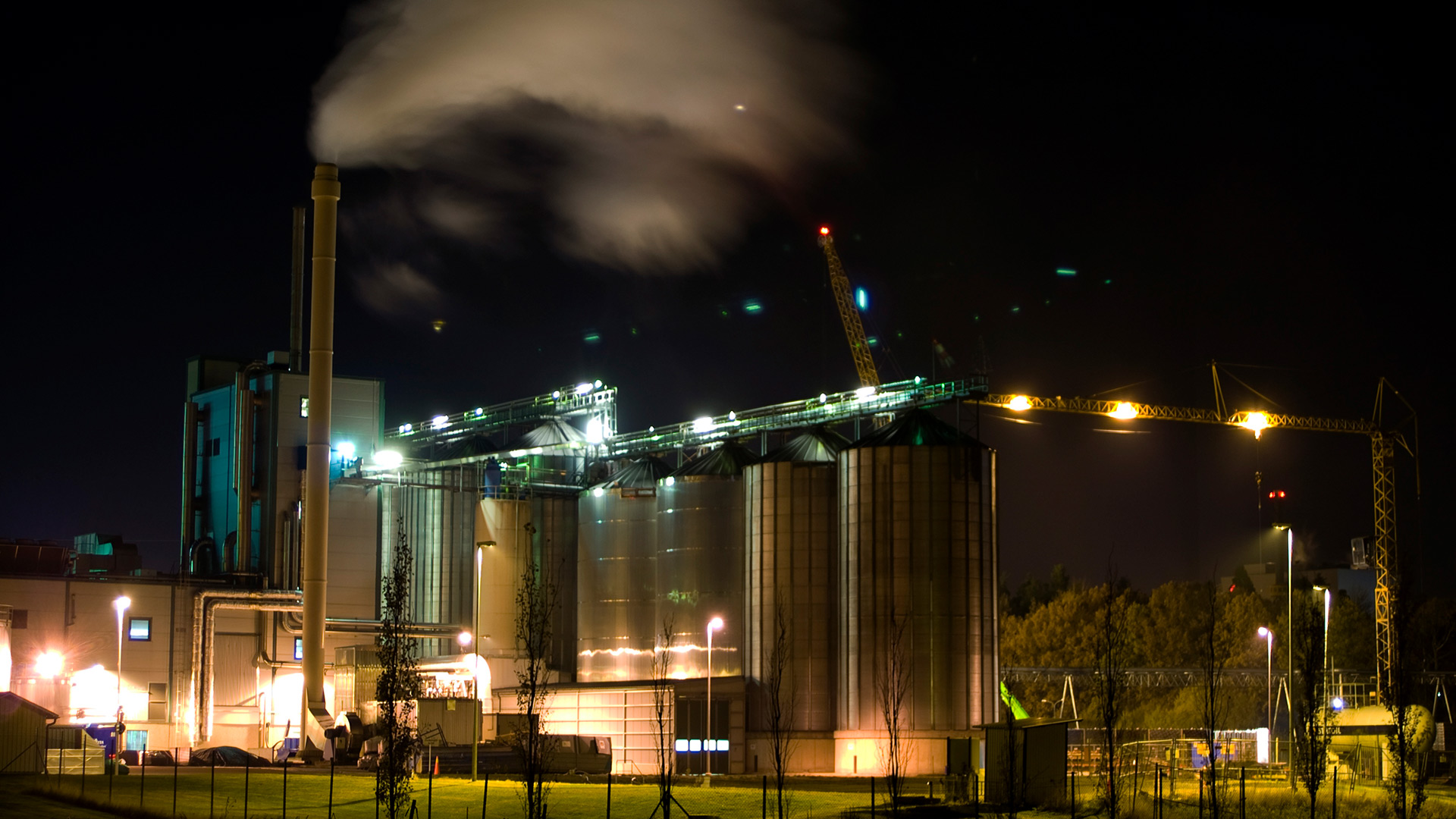



“Enercon has been working with EQS Global for 4 years and so far the balance has been more than positive. Competitive pricing of services, trust, professionalism, and safety are the reasons why we are and will continue to be partners of EQS Global.”

“Until now Águas do Norte has contracted the services of condition assessment, predictive evaluation and monitoring to the EQS Global and the balance has been frankly positive. The mais challenges in our industry are to organise, collect, make available and process information with maximum added value. And EQS Global has been an important partner to overcome these same challenges.”

“GE Gas Power has been working with EQS Global for 8 years. Our first experience came in 2012 and since then we have been working on several projects in with GE participates as the main business partner in the maintenance of turbines for power generation for clients such as EDP Produção and GALP Energia. The balance os this partnership with EQS Global is very positive, for us and our clients.”

Success Stories
Our deep industry knowledge, software, hardware, and R&D capabilities enable EQS Digital to design and implement end-to-end digital strategies.
Get in touch with
EQS Digital team!
Let us demonstrate how our digital solutions can help you and your company. Please complete the form to send us a message.